데이터 분석과 AI 등 기술로 사전에 문제를 감지해 대처하는 것으로 가동 시간을 40% 단축할 수 있다
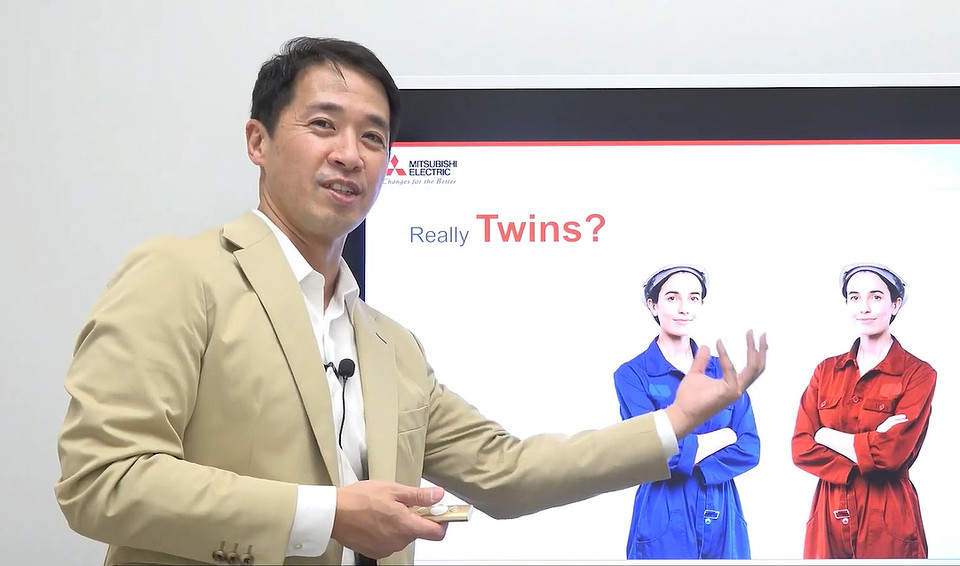
지난 16일, 인공지능신문, 테크데일리, 전자신문인터넷이 공동주최한 제5회 인더스트리 4.0 디지털 인사이트 2021 컨퍼런스가 'ID4.0, 지능형 제조, 생산시스템 디지털 전환과 DX 구현 전략'이란 주제로 1000여명이 참가한 가운데 온라인으로 진행됐다.
코로나 이후, 제조 4.0 분야는 인공지능(AI), 로봇을 비롯한 머신에서 자율 생산과 제어가 가능한 스마트팩토리 구현을 위한 유연한 초고속 네트웍, 엣지 및 데이터, 산업제어 IT/ OT솔루션 등 인프라 통합을 통한 제조, 생산, 유통, 운영에 이르기까지 에너지, 효율성,생산성 등을 위한 디지털 혁신과 새로운 비즈니스 기회를 만들어 가고 있다.
이날 컨퍼런스에서는 이를 구현하기 위한 다양한 솔루션과 관련 인사이트를 공유했다. 한국미쓰비시전기오토메이션 스기야마 하지메 그룹장의 발표 내용을 요약해 본다.
미쓰비시전기는 2003년부터 e-F@ctory(이팩토리)라는 콘셉트를 제창해 왔다. FA(공장자동화) 기술과 IT(정보기술)을 활용함으로써 개발∙생산∙유지보수 전반에 걸친 전체 운영 비용을 줄이고, 제조 디지털 혁신과 고객의 시스템 개선활동을 지속적으로 지원하고 있다.
요즘 가장 뜨거운 토픽은 '디지털 트윈'과 '탄소 중립'이다. 이들 테마가 왜 제조업에서 주목받고 있고, 왜 모든 기업이 도입해야 할까.
디지털 트윈을 사용하기 시작한 이유는 글로벌 경쟁이 날로 심화되고 있기 때문이다. 속도의 중요성이 점점 더 커지고 있다. 인공지능(AI)과 사물인터넷(IoT) 등 과거에는 없던 기술이 속속 등장하면서 설계시간을 단축하는 등 제조와 설계 공정을 더 빠르게 할 수 있게 됐다
프로그래밍도 마찬가지다. 디지털 트윈을 활용하면 유지관리 시간도 줄어들고, 데이터 분석을 활용해 공장에서 해결해야 할 문제를 더 빨리 파악해 대응할 수 있게된다. 제조라인을 구축하는데 필요한 기계 설계에서부터 디지털 정보 공유 및 유지보수에 이르기까지 아주 쉽고 빠르게 검증할 수 있다.
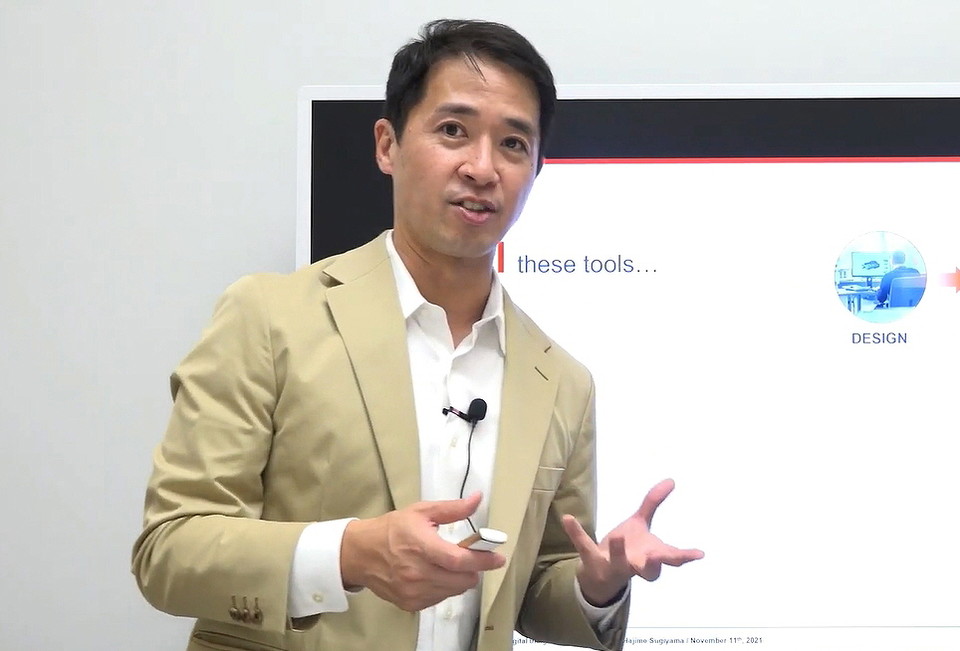
데이터 분석과 AI 등 기술로 사전에 문제를 감지해 대처하는 것으로 가동 시간을 40% 단축할 수 있다고 한다.
하지만 디지털 트윈을 공장에 구현해 원격관리하는 일은 쉽지 않다. 생산라인이나 기계적 결함 등 경고를 받고 현장에 출동해보면 다른 부분에서 문제가 발생한 것이라 보수 준비를 다시해와야 하는 경우가 발생하기도 한다. 모니터링으로 보는 것과 실제 현장이 다른 것이다. 이렇게 되면 애써 구축한 디지털 트윈이 무용지물이 된다.
프로그램이 워낙 다양한 때문이다. 세계 각국에서 서로 다른 프로그램을 만들고 이를 서로 다른 나라에서 사용한다. 생산라인은 동일한 것을 사용해도 프로그램이 다르면 불일치가 많이 발생한다.
디지털 트윈은 첫걸음이 중요하다. 어떤 데이터를 먼저 다룰 것인지 우선순위를 정해야 한다. 그 다음에 보다 진화된 디지털 트윈 단계로 나아갈 수 있다. 제품을 설계하는 동시에 공급망과 연계하는 연결 부분도 동시에 만들어야 한다.
그래야 주문이 들어오자마자 생산을 시작할 수 있다. 생산라인에서는 설비나 기계보다는 부품을 옮기는 과정에서 더 많은 장애요인이 발생한다. 디티털 트윈으로 사전에 문제가 어디에 있는지 무엇을 개선해야 하는지 알아 볼 수 있다.
앞으로는 기업들이 탄소중립 의무를 충족하지 못하면 시장에 진입조차 하지 못하게 된다. 탄소중립은 제조업과 밀접한 관계에 놓이게 됐다.
이산화탄소 배출을 줄여야 한다. 그러나 탄소중립은 이산화탄소 배출을 줄이는 것만으로는 해결되지 않는다. 청정에너지 사용을 늘리는 것이 한가지 방법이다.하지만 청정에너지 시설을 갖추는 것은 현실적으로 어렵다.
태양전지 등을 설치하면 되지만 비싸다. 에너지 절약이 최선책이다. 에너지는 생산성을 높이면 절약할 수 있다. 불량률을 줄이고 품빌으 높이면 생선성이 오르고 에너지는 절약하게된다.
기본에 충실하는 것이 중요하다. 미쓰비시는 에너지 소비를 줄이는데 초점을 맞추고 있다.