예측 유지보수는 사전 예방적이며, 이것이 바로 스마트 모니터링 시스템이 제공하는 것으로 운반 장비에 대한 데이터 기반 분석을 통해 잠재적인 결함을 조기에 식별하고 방지하여 최적의 차량 생산 프로세스를 유지...이 AI 지원 시스템은 레겐스부르크 공장에서만 차량 조립 과정에서 연간 평균 약 500분(약 526대 조립시간)의 중단 시간을 방지한다
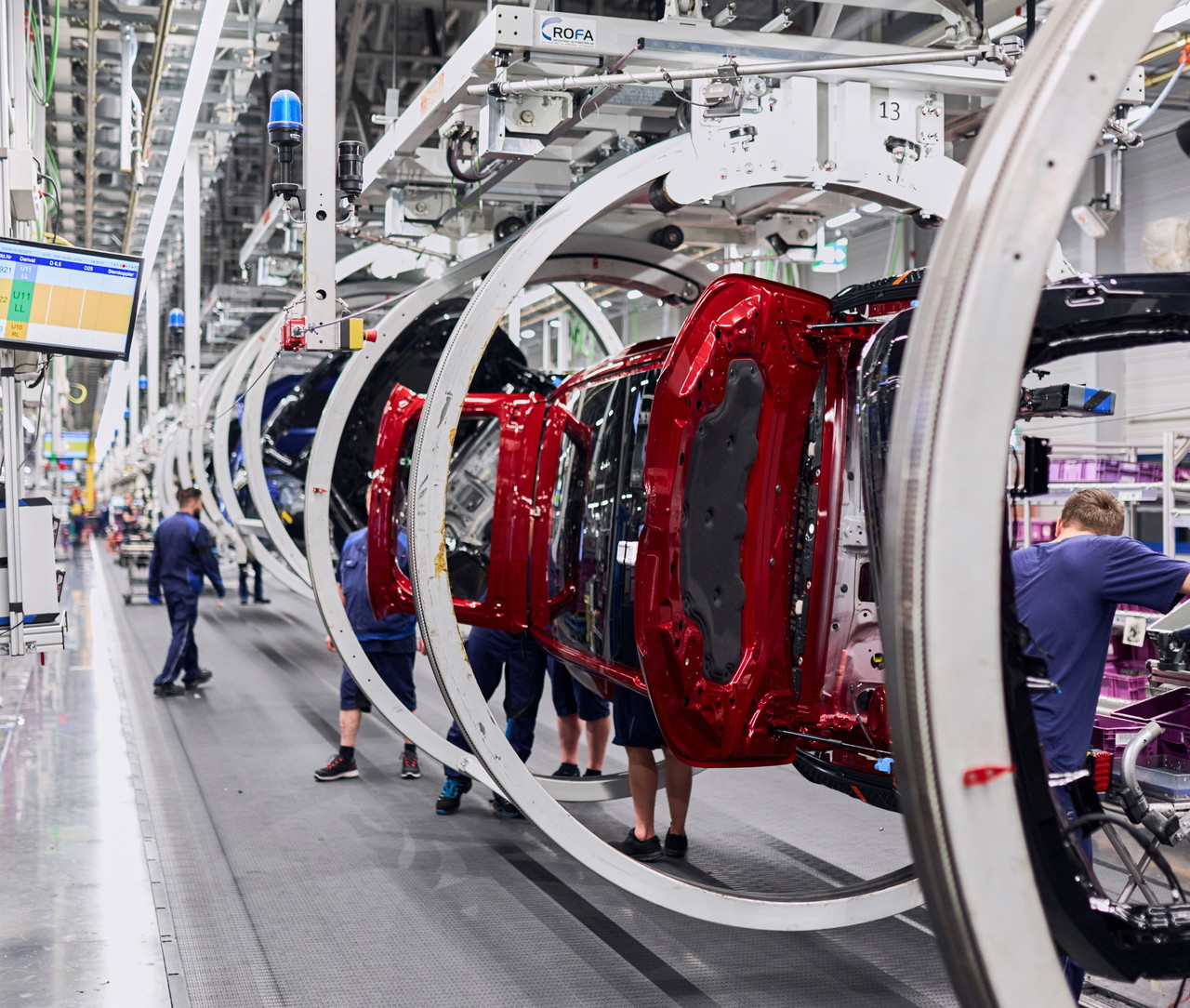
인공지능을 통해 계획되지 않은 공장 가동 중단이 발생하기 전에 방지하는 것이 BMW 독일 바이에른 주 레겐스부르크 공장(BMW Group Plant Regensburg. 이하, 레겐스부르크) 조립공정에서 사용되는 스마트 분석 시스템의 목표다.
예측 유지보수는 사전 예방적이며, 이것이 바로 스마트 모니터링 시스템이 제공하는 것으로 운반 장비에 대한 데이터 기반 분석을 통해 잠재적인 결함을 조기에 식별하고 방지하여 최적의 차량 생산 프로세스를 유지할 수 있다.
BMW의 이 인공지능(AI) 지원 시스템은 레겐스부르크 공장에서만 차량 조립 과정에서 스마트한 유지보수로 연간 평균 약 500분의 중단 시간을 방지한다고 한다.
잠재적인 중단에 대한 더 빠르고 예방적인 대응을 위한 데이터 분석
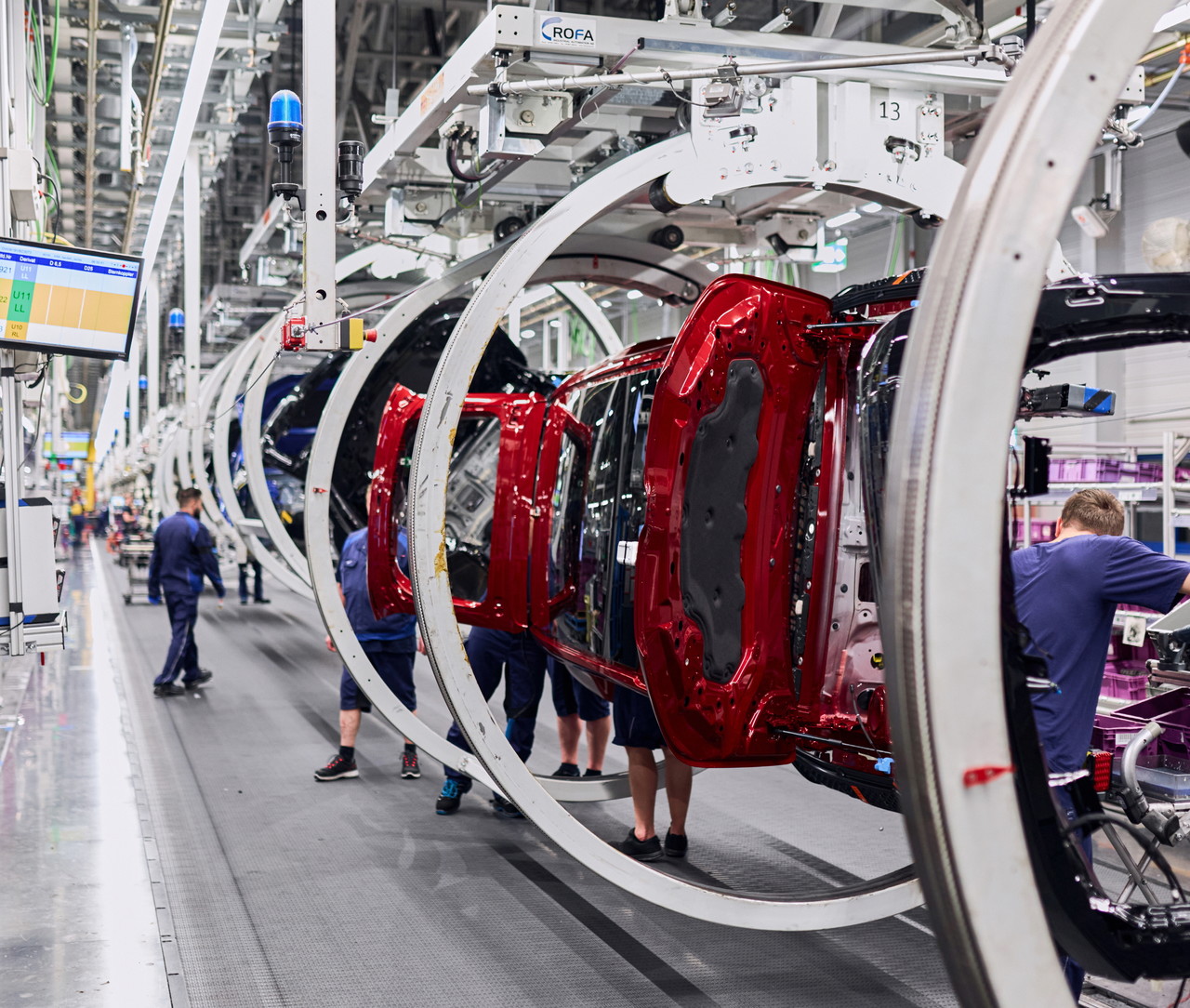
레겐스버그에서 조립하기 위해, 차량들은 일반적으로 체인으로 생산 홀을 통과하는 이동식 로드 캐리어 또는 스키드 시스템에 부착된다. 최첨단 컨베이어 시스템의 기술적 결함은 조립 라인을 정지시킬 수 있는데, 이는 더 많은 유지보수 노력이 필요하고 결과적으로 더 높은 비용을 초래한다.
이러한 일이 발생하지 않도록 레겐스부르크의 혁신 팀은 잠재적인 기술적 결함을 조기에 식별하여 생산 손실을 미연에 방지할 수 있는 시스템을 개발했다. 영향을 받은 컨베이어 부품 및 장비는 생산 라인에서 분리되어 수리된다. 이 모니터링 시스템의 장점은 추가 센서나 하드웨어가 필요하지 않으며 설치된 구성 부품 및 장비 등 컨베이어 요소 제어의 기존 데이터를 평가한다는 것이다. 이상 징후가 발생되면 경보로 알려준다.
예를 들어, 조립을 통해 차량을 운송하는 데 사용되는 로드 캐리어는 다양한 데이터를 캐리어 제어 시스템으로 보낸다. 그런 다음, 이 데이터는 공장 제어 시스템을 통해 BMW 그룹의 자체 예측 유지 관리 클라우드 플랫폼으로 전송된다. 여기서부터 분석이 시작되며, AI 알고리즘은 전력 소비량의 변동, 컨베이어 구동 움직임의 이상, 바코드 가독성이 떨어지는 등 오작동을 유발할 수 있는 이상 징후를 실시간으로 탐색하여 이상 징후가 발견되면 유지보수 제어 센터에서 경고 메시지를 수신하고, 이를 근무 중인 유지보수 기술자에게 전달된다.
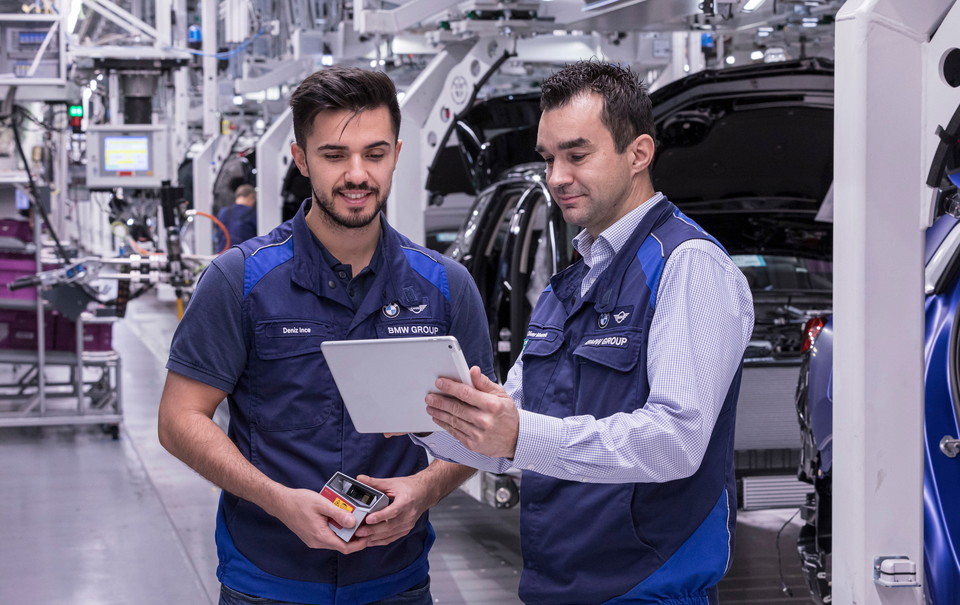
BMW 레겐스부르크 공장 프로젝트 관리자인 올리버 마섹(Oliver Mrasek)은 “저희 제어 센터의 감시 모니터는 연중무휴 24시간 운영됩니다”라며, "이를 통해 우리는 조립 라인에서의 모든 종류의 결함 보고에 신속하게 대응하고 영향을 받은 차량은 조립 공정에서 제외할 수 있습니다"라고 설명했다.
AI 지원, 표준화 및 비용 효율성
또한 올리버 마섹은 예측 유지 관리가 독립형 솔루션이 아니라고 강조한다. "이 시스템은 BMW 그룹의 중앙 작업 현장 관리 및 기타 공장 현장과의 협력을 통해 표준화되어 전 세계 다른 BMW 그룹 공장으로 신속하고 간편하게 배포할 수 있습니다“라며, "이 접근 방식은 비용 효율적이며, 시스템은 추가 센서가 필요하지 않으므로 스토리지와 컴퓨팅 성능에 드는 비용만 발생됩니다"라고 강조했다.
이어 그는 "자체 개발한 머신러닝 모델도 시스템에 구현되었는데, 이 모델은 다양한 이상 징후를 다양한 색상으로 표시하는 이른바 히트맵을 사용하여 모델의 결과를 시각화합니다"며, "이를 통해 다양한 구성 요소의 다양한 오류 패턴을 매핑하고 목표에 맞는 방식으로 대응할 수 있습니다"라고 덧붙였다.
특히 이러한 실제적인 데이터를 바탕으로 AI 알고리즘은 지속적으로 개선된다. 이 팀의 데이터 과학자인 데니즈 잉스(Deniz Ince)는 "최적의 예측 유지 관리는 비용을 절약할 뿐만 아니라 계획된 수량의 차량을 제 시간에 맞춰 제공할 수 있음을 의미합니다"라며, "이는 생산 스트레스를 크게 줄여줍니다"라고 말했다.
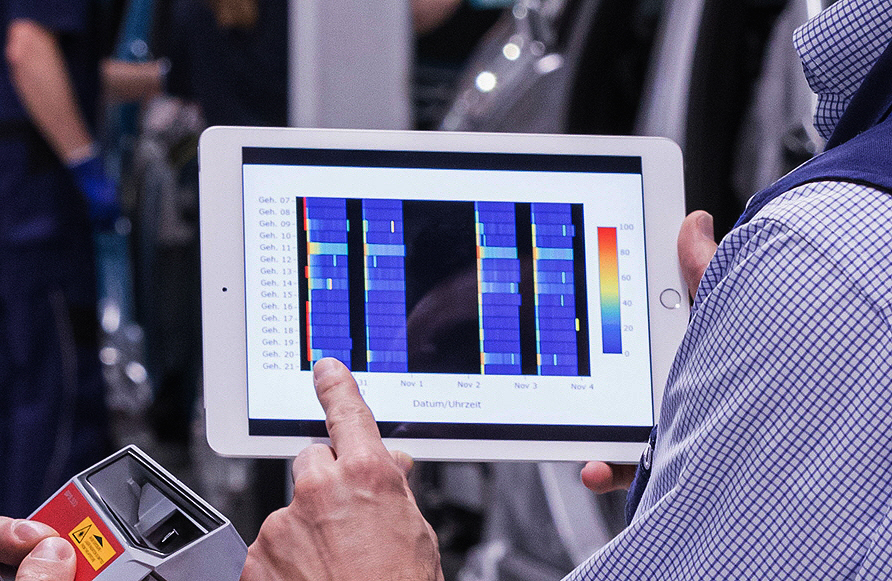
올리버 마섹과 그의 팀원들은 지난 6년 동안 컨베이어 기술의 데이터 기반 모니터링 작업을 진행해 왔다. 오늘날 주요 조립 라인의 약 80%가 이미 이러한 방식으로 모니터링 되고 있다. 물론 모든 결함을 미리 감지하거나 예방할 수는 없다. 하지만 현재, 자동차 조립 라인에서만 연간 최소 500분(약 526대 조립 시간)의 가동 중지 시간을 방지하고 있다.
BMW 레겐스부르크 공장에서는 차량이 대략 1분마다(정확히 말하면 57초마다) 조립 라인을 거치고 있다. 이 시스템은 이미 딩골핑(Dingolfing), 라이프치히(Leipzig), 베를린(Berlin) 공장 현장의 컨베이어 시스템에 적용되고 있다.
BMW 그룹의 이 시스템의 목표는 '결함 감지'와 '잠재적 정지' 사이에 남은 시간을 추정하는 시스템 학습을 통해 인공지능의 가능성을 더욱 활용하는 것이다. 이는 기술자가 유지 관리를 얼마나 빨리 수행해야 하는지 결정하고 필요한 경우 우선순위를 정하는 데 도움이 된다. 또한 레겐스부르크 공장의 다른 영역에서도 더 많은 능력을 기대하고 있다. 예를 들어, 차량에 브레이크액과 냉각수를 채우는 데 사용되는 장비에 이 시스템을 사용할 수 있는지 여부를 현재 테스트하고 있다.
한편, 인공지능을 통한 예측적 장비 유지보수를 위한 다양한 옵션이 이미 존재하지만, 레겐스부르크의 ‘통합 학습(Integrated Learning)’ 시스템은 지금까지는 최초의 시스템으로 BMW 그룹은 이 시스템의 자체 개발에 대한 두 가지 특허를 등록했다고 한다.